
INDUSTRIAL AUTOMATION
Industrial Automation comprises the use of technological solutions, such as software, hardware, electromechanical machines and specific equipment, to automate and optimize industrial processes. High Power, through years of experience in the Industry, carries out projects aimed at automating industrial processes involving the areas of mechanics, electrical and automation technologies. With a team of qualified and certified professionals, we are able to provide solutions that integrate production areas.

click

INDUSTRIAL AUTOMATION LEVELS
Today, we can look at the concept in different ways: Its application is vast, and can occupy many more places than the factory floor and the company's core activity. At global levels, we can consider 4 types of automation:
● Operational automation: intelligent machines and sensors that monitor operational performance, collecting data that helps managers in decision-making.
● Control automation: programmable devices (PLCs or CNCs, for example) inserted into devices, equipment and machines that then apply operational logic to programmed processes.
● Supervisory automation: systems that monitor data and readings obtained from sensors and controllers.
● Informational automation: a system that integrates the entire flow of information from other layers of industrial automation, in a way that organizes them to facilitate general control of operations.
INDUSTRIAL AUTOMATION MODELS
We consider 3 defined Industrial Automation models suitable for different production objectives: Fixed Automation, Programmable Automation and Flexible Automation.
Fixed Automation: it is most suitable in mass production lines and continuous production lines. The main characteristic in Fixed Automation is the rigidity of the equipment configuration, since once a control configuration is created, it is not possible to change it without completely reconfiguring the equipment and systems. The main aspect is the high production rate, although there is a need for a larger initial investment in specific equipment. Recommended for long production periods of a specific item.
Programmable Automation: In this automation model, more profitable levels are achieved in the long term, as it allows items with the same characteristics to be produced per batch. They are programmable and customizable systems that can be adapted to the needs of each type of part produced. Programmable automations are especially suitable for product changes and for industries with seasonal products.
Flexible Automation: In this automation model, it is possible to make changes to product design quickly and easily, facilitating production diversity. There is no need to use a batch system and there are cases where it is possible to produce just one piece, if desired. In this model we have greater capacity to adjust programs and physical elements of manufacturing without loss in productivity. In a flexible automation system, through automatic control equipment, great flexibility is achieved for modifications in the product design. These changes can be made quickly through commands provided via code by operators.
Projetos Elétricos e Mecânicos
When the company decides to implement Industrial Automation processes, it is unnecessary to state the need to prepare Engineering Projects to achieve the basic objectives of automation, which is to increase productivity with better use of raw materials and reduce production costs of a general form. Under the scope of Industrial Automation, projects are divided into: Electrical Project and Mechanical Project, the latter covering the areas of mechanics itself, hydraulics and/or pneumatics.
Ex: Mechanical Project

Ex: Hydraulic Project

Ex: Pneumatic Project


Ex: Electrical Project
Assembly of Frames and Panels
Industrial Automation Electrical Boards and Panels are structures assembled to meet the needs of energy distribution for the control of machines, equipment, motors, drives, controllers, HMIs and also for activating devices. Panels and frames can be classified into: Distribution Panels, Control Panels, Process Control Panels and Automation Panels. Each type is designed to meet specific functions, from energy distribution to precise supervision of industrial processes. Furthermore, from an electrical point of view, the panels can be:
General Low Voltage Switchgear (QGBT)
Engine Control Center (CCM)
Electrical command and control panel
Industrial electrical distribution panel
Panel for drives

Distribution Panel
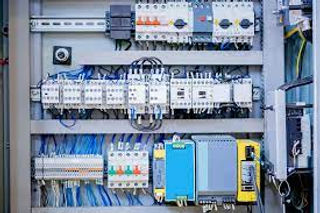
Control panel

Process Control Panel
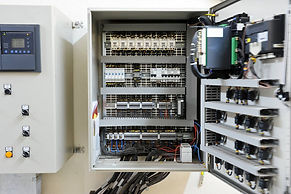
Automation Panel
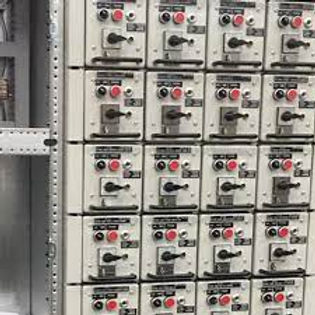
General Low Voltage Board (QGBT)
Electrical, Mechanical and Hydraulic Installations
One of High Power's qualifications in providing services to Industry is, without a doubt, its Know-How in Industrial Installations. With qualified technical staff in the areas of Electrical, Mechanical, Hydraulic and Pneumatic, our coverage involves the complete processes of a factory floor implementation. Transfers, Disassembly/Assembly of machines and equipment, NR10/NR12 adjustments, load sizing, commissioning and startup, in addition to other functions, are part of the High Power Service Scope.

Electrical Installations

Mechanical Installations
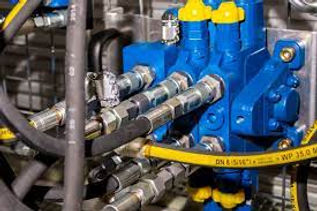
Hydraulic/Pneumatic Installations
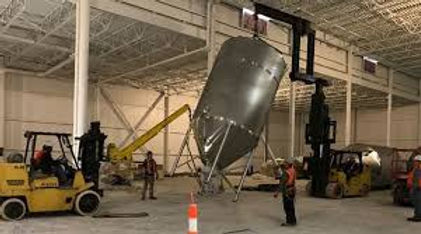
Assembly/Disassembly/Transfer of Machines
Programming (PLC's, CNC, HMI)
One of the components of the Industrial Automation process, as a consequence of the insertion of Hardware and Software technology, is the adoption of programming tools that make production processes more efficient by controlling and monitoring routines and instructions. Among the solutions developed we can highlight: PLC Programming (Programmable Logic Controller), HMI Programming (Human Machine Interface) and CNC Programming (Computer Numerical Control).
The hardware device known as PLC is nothing more than a computer designed to work in extreme industrial conditions and aggressive environments, in order to withstand dust, high temperatures and vibrations. In PLC Programming, this specialized computer was designed to optimize the control and monitoring of specific operations inherent to the industrial environment. It is no exaggeration to say that without the PLC, there is no automation.
In the case of HMI Programming, the resource acts as a mediator of the interaction between an operator and an automation system. In industry, it is generally used in production lines and machines for various purposes. In a typical industrial automation system, there is a central PLC responsible for collecting data from sensors and other field devices. The basic function of the HMI is to access the PLC, read the collected data and project it visually so that the system operator can make a decision based on the real situation of the machine or process. After making the decision, the operator can issue a command to the HMI so that it goes the opposite way, taking information to the PLC so that it can then change some aspect of the control system.
In the case of CNC Programming, programming instructions aim to create instructions or codes used to control machines that have computer numerical control (CNC). CNC machines are automated manufacturing tools that perform precise and complex operations on a variety of materials, such as turning, cutting, milling and drilling. CNC programming creates program instructions for computers that control a machine/tool improving manufacturing processes. G codes direct the movement and function of the machine, while M codes direct operations outside of the movements. The G code activates the CNC machine while the M code activates the machine's programmable logic controller. The main characteristic of machines equipped with Numerical Control is precision. For a three-dimensional system, three perpendicular axes (90º) to each other are used, which are designated using the fingers of the right hand: Thumb - X axis. Indicator - Y axis. Middle - Z axis.CNC, IHM)
PLC Programming - Ladder Language

HMI Programming
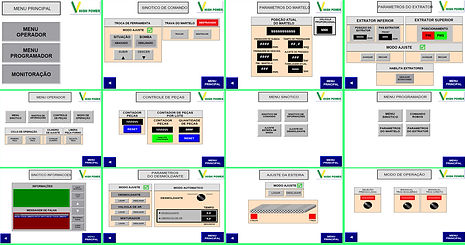
CNC Programming


